|










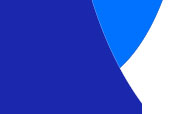 |
Les
résines
Il
existe au moins une centaine de résines. Parmi celles-ci,
3 rentrent dans la catégorie des thermodurcissables
:
Le
polyester, l’époxy, le polyuréthanne.
Nous
allons surtout parler de l’époxy pour
sa facilité de
mise en oeuvre, ses qualités mécaniques, sa polyvalence
et sa parfaite application dans le domaine du bricolage nautique (pour
ce qui nous
concerne) que ce soit en utilisation exclusive (coque moulée),
en stratification sur bois ou en collage (west system).
Le
polyester
Il est surtout destiné à la construction de grandes pièces
où l’utilisation de l’époxy multiplierait le coût
de revient par 3 ou 4 sans rapport avec le gain de qualité mécanique.
Il a de plus 2 gros défauts : son fort rétrain (7%) et son très
bref pot life (temps pendant lequel il est possible de le travailler avant
le gel).
La polyuréthanne
Elle surtout utilisée comme colle, base de mousse, base de peinture,
support de charges pour enduits ...
L’époxy
Revenons donc à notre époxy, cette résine a des qualités
mécaniques propres, une facilité de mise en oeuvre et une polyvalence
qui la rendent inégalée.
Seul son prix peut la mettre en difficulté face à d’autre
matériaux à qualité voisine (alu, titane, …).
Mise
en oeuvre:
L’époxy présente tellement de variante (à cuire,
tissus préimprégné, pour inclusion, pour stratification,
...) que nous allons nous limiter aux 3 usages les plus fréquemment
usités dans notre domaine d’application
l’utilisation en moulage ;
la stratification sur bois ;
la fabrication de colles et d’enduits.
L’utilisation
en moulage de l’époxy nous fera choisir
une résine à fort pouvoir mouillant et
donc d’une
bonne viscosité (environ
1500 mPa/s) et d’une faible densité (environ 1,10
g/cm3).
Nous
lui choisirons un durcisseur permettant lui donnant
un pot life d’environ
3h.
Selon
le type de pièce et les qualités mécaniques
qu’elle
devra posséder (type d’efforts demandés,
type de contraintes appliquées, ...) nous lui choisirons,
en renfort, des tissus de type (verre, kevlar, carbone), à armature
(roving ou taffetas, taffetas câblé,
sergé, toile, bibiai, ...) de poids (gr/m²),
en quantité suffisante
afin d’obtenir un échantillonnage respectant
ce cahier des charges.
Les
diluants et les solvants
Il sont souvent confondus
ou utilisés l’un
pour l’autre
Si les diluants entrent
dans la catégorie des adjuvants,
ce n’est surtout pas le cas des solvants qui,
comme leur nom l’indique, dissolvent. Je pense
particulièrement à l’acétone
utilisé à tort et à travers.
Les adjuvants
Sous le terme « adjuvant », se retrouve tous
les produits que l’on ajoute à une résine
pour en modifier les caractéristiques.
-
Pour l’époxy, le principal adjuvant
est son durcisseur.
Adressez-vous à votre fournisseur pour définir
celui dont vous aurez besoin car il en
existe tellement de types qu’il serait sans intérêt
de les nommer ici.
Chaque
fabriquant en propose plusieurs pour chaque type d’époxy
-
Pour
le polyester par contre, les adjuvants sont assez nombreux
:
le Styrène, qui est l’une des bases de cette
résine, peut être ajouté pur
pour liquéfier
la résine. (Ce n’est utile
que dans des cas bien particulier et
je déconseille à des
bizuth de l’utiliser)
Il existe
aussi du styrène paraffiné.
Ajouté au
gel coat, il lui permet de sécher à l’air
et donc d’être utilisé comme
gel coat de finition (Top coat) pour
effectuer des retouches une
fois la coque démoulée.
Vous pouvez aussi utiliser de la
paraffine liquide.
Le catalyseur
appelé PMEC (Péroxyde de Méthyl
Ethyl Cétone, le Butanox
M50 le plus connu) ajouté à la
résine accélérée
déclenche
l’effet de chaleur qui
va engendrer le durcissement,
doit être incorporé à la
résine à raison
d’environ 2% (+ ou -
0,5%). A ce taux là,
la résine à déjà un
rétrain
de 7%.
Trop l’augmenter ferait beaucoup augmenter le rétrain
ainsi que la chaleur et ferait craqueler la résine.
L’accélérateur introduit dans la résine
vierge soit chez le fabriquant (résine pré-accélérée),
soit par vos soins, permet, lors de l’introduction
du PMEC de déclencher l’effet
de catalyse.
Il s’agit de l’octoate de cobalt (couleur mauve) à raison
d’environ 0,2%. Il peut être augmenté l’hiver par faible
température de travail. D’où l’importance de faire
un essai de pot life tous les jours pour affiner ces 2 variables (accélérateur
et catalyseur).
-
Le Xylène
est le diluant du polyuréthanne
en général, que ce soit en enduit
ou en peinture (jusqu’à 50%).
Résumé
N’utilisez l’acétone que pour le nettoyage
des outils et ceci loin du plan de travail. Les solvants
dissolvent et les diluants diluent. Pour l’époxy,
le meilleur solvant est l’alcool à brûler
(faible coût et bonne volatilité), pour le
polyuréthanne le solvant est le trichloréthylène.
Un
dernier point en ce qui concerne les
charges et enduits
Dans
la fabrication d’un enduit ou d’une
charge (joint-congés), il est donné pour
chaque type de charge ou d’enduit une densité maximum
en gr par litre de résine (mélange).
L’incorporation
de la charge doit se faire dans le mélange
résine/durcisseur
et ceci de façon régulière
sans cesser de remuer le mélange.
Le pot life de l’ensemble
est sensiblement plus long que pour une résine
seule.
-
Stratification
sur bois gras ou résineux
Dans le cas
de stratification sur un bois gras ou résineux (acajou et
pin par exemple), l’accrochage de la résine DANS le bois (pas
seulement « sur » le bois) est très mauvais. Un truc consiste à passer,
avant la résine, un produit qui va pénétrer le bois et
favoriser cet accrochage. Pour le polyester, le produit est à faire
soi-même avec de l’acétone et de l’octoate de cobalt
(accélérateur du polyester de couleur mauve) mélangés à raison
de 100 parts d’acétone pour 20 parts d’octoate de cobalt.
Vous allez obtenir un mélange rosé très volatile que vous
passerez au pinceau sur toute la surface à stratifier, le séchage étant
presque instantané, le temps de préparer votre résine
et vous pouvez commencer. Pour l’époxy, le produit est pratiquement
tout fait car il s’agit de passer une couche de peinture polyuréthanne
diluée à 50%. Ici, il vous faudra attendre le séchage
de la peinture et un léger ponçage avant de débuter
la stratification.
-
La suite, un jour ou j’aurai
le temps…
|
|
|